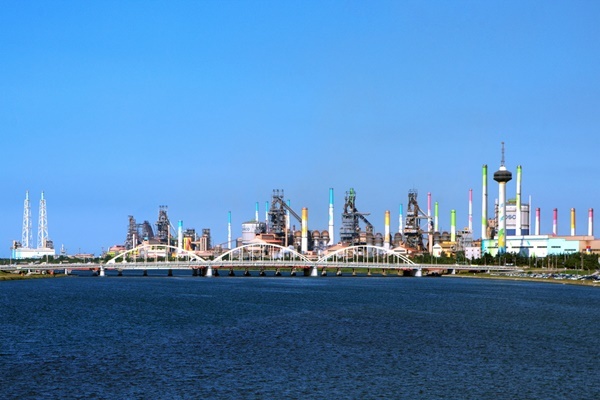
포스코 포항제철소 전경. /사진=포스코 제공
[미디어펜=권가림 기자] 포스코가 생산부터 재활용까지 생애주기적 관점에서의 철강 신소재 개발 및 상용화를 통해 대체소재 확산을 막고 친환경경영에 앞장서고 있다.
29일 업계에 따르면 포스코는 철강제품의 생산과 사용, 폐기, 재활용까지 제품의 전생에 걸친 친환경성 측면인 라이프 사이클 어세스먼트(LCA: Life Cycle Assessment) 관점에 중점을 두고 있다.
최근 탄소섬유, 플라스틱, 알루미늄 등 철강소재를 대체하는 다양한 소재가 사용되고 있으나 LCA관점에서 보면 철강의 친환경성에 대한 경쟁력이 부각되기 때문이다.
철강을 생산할 때 철광석과 석탄, 전기 등의 다양한 자원과 에너지가 필요하다. 하지만 그 과정에서 생성되는 부산물의 재활용, 최첨단 철강소재를 사용한 제품의 에너지효율 증대 및 철강의 재활용성 등 전체 라이프사이클을 감안하면 철강 제품이 친환경적이라는 것을 알 수 있다.
철강은 자동차, 선박, 건축물 등에 사용되는 가장 기초적인 전통 소재로 가공성·용접성이 뛰어나고 경제적이다. 또 도금을 통해 녹 발생을 쉽게 방지할 수 있고 재활용이 쉬운 친환경 소재다.
경제성·경량화·안전성 우수 '기가스틸'
이에 포스코는 경제성, 경량화, 안전성, 친환경성에서 높은 평가를 받고 있는 ‘기가스틸’을 개발했다.
기가스틸은 1㎟ 면적당 100㎏ 이상의 하중을 견딜 수 있는 차세대강판으로 양쪽 끝에서 강판을 잡아당겨서 찢어지기까지의 인장강도가 980MPa(1기가파스칼) 이상이다. 가로 10cm, 세로 15 cm의 손바닥만한 크기인 ‘기가스틸’에 약 1톤 가량의 준중형차 1500대를 올려놓아도 견딜 수 있다.
기가스틸은 알루미늄 등 대체소재에 대비해 경제성, 경량화, 강도는 물론 재활용성, 제품을 생산할 경우 상대적으로 CO2배출량이 낮아 친환경성 측면에서도 월등한 효과를 낼 수 있는 것이 특징이다.
‘기가스틸’을 자동차 소재로 적용할 경우 차량 무게가 가벼워져 연비가 개선되거나 이산화탄소 배출을 줄일 수 있는 장점도 있다. 세계철강협회 자료에 따르면 소재 1kg를 생산할 때 탄소배출량은 철의 경우 2.0~2.5kg인 반면 알루미늄은 11~12.6 kg으로 5배가 넘게 차이난다.
자동차로 생산된 이후에도 제품 수명주기를 감안한 누적 온실가스 배출 역시 약 10%가량 적어 철강제품이 전체 온실가스 배출에 있어 친환경적인 것으로 알려졌다.
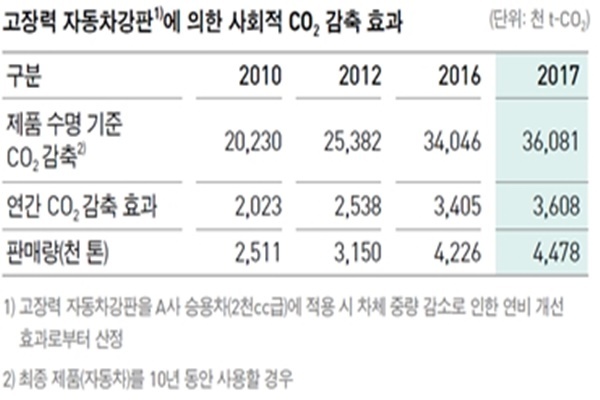
고장력 강판은 연비 향상과 연간 CO2 감축 효과를 낼 수 있다. /사진=포스코 제공
'자동차 경량화·온실가스 배출 감소' 고장력강판
자동차 경량화는 연비 향상과 온실가스 배출 감소를 위한 대표적인 기술이다. 차종별로 다소 차이가 있으나 자동차의 중량을 10% 감소시킬 경우 5~8%의 연비 개선효과가 있어 그 만큼 이산화탄소 배출량을 낮추는 것으로 관측됐다.
고장력 자동차강판은 얇은 두께로 두꺼운 일반 강판과 같은 강도를 얻을 수 있어 가벼운 차량 제작이 가능하며 동시에 에너지 효율을 높일 수 있다.
고장력 강판으로 제조한 승용차의 연간 주행거리를 1만9000km로 가정(승용차 연간 주행거리 (교통안전연구원, 2006))하고 10년간 운행할 경우 차량 1대당 간접적으로 약 1.8톤에 달하는 CO2 감축 효과를 거둘 수 있을 것으로 보인다.
에너지 고효율 전기강판 'Hyper No'
포스코의 에너지 고효율 전기강판 Hyper NO는 주로 고효율 모터에 적용돼 전기자동차의 연비를 향상 시킬 뿐만 아니라 자동차의 성능을 높여줄 수 있는 핵심 소재다.
또 냉장고, 청소기 등 고효율을 요구하는 가전제품과 풍력발전기, 산업용 발전기 등을 만들기 위한 고효율의 모터에 필수적으로 적용되는 철강재다.
포스코는 최근 접착제와 같은 기능을 하는 코팅을 전기강판 표면에 적용하는 이른바 ‘셀프본딩’기술도 개발했다. 코팅된 Hyper NO강판 수 십장을 쌓아 일정 수준의 열처리만 거치면 자체적으로 결합되도록 하는 기술이다.
셀프본딩 기술을 적용하면 용접 등의 물리적인 방식과 달리 전기강판의 전자기적 특성을 저하시키지 않아 모터효율을 향상시킬 수 있다. 또 기존 용접 체결방식 대비 모터코어의 철손이 10% 이상 줄어든 효과도 낼 수 있다.
[미디어펜=권가림 기자]